Unlocking the potential of lithium extraction and purification
As the demand for lithium-ion batteries rises, the importance of efficient and sustainable lithium mining practices is essential. OLI offers consulting services to optimize lithium mining and refining. Our experts provide industry-leading solutions that maximize ROI and reduce environmental impact.
Effective lithium extraction and purification
Extracting lithium poses many challenges however OLI Systems' team of experts provides multiple levels of consulting to design effective lithium extraction processes from brines or hard rock sources. Understanding the chemical behavior behind each process step enables efficient and sustainable production and enables engineers to maximize yields and increase purity levels. By accurately predicting mass balance, minimizing water and chemical requirements and addressing regulatory questions using first-principles thermodynamics, our services help operators gain increased efficiency, achieve regulatory compliance and lower costs.
Trusted partner
Optimize process design and operations for lithium extraction and refining
Extracting lithium from saline lakes, direct lithium extraction and hard rock pose unique challenges to operations efficiency and sustainability from a design and operations standpoint. These challenges can be overcome by developing optimized process designs at the front end of the project followed by proactive troubleshooting and monitoring to ensure seamless operations. OLI Systems’ consulting team is available to help operators to achieve optimal outcomes in water and chemical treatment, product purity and lithium recovery.
Salar brine evaporation
A complex process that requires expert design to maximize product recovery while minimizing chemical addition. OLI consultants provide comprehensive support to clients, from evaluating salt precipitation during evaporation to identifying the formation of key elements like Li, K, and B. We design evaporation operations in steady-state and dynamic mode, based on specific needs. The end result is a process design that takes into account seasonal effects and changes in inflow compositions, ensuring maximum product recovery with minimal chemical intervention.
Direct lithium extraction (DLE)
OLI consultants have the expertise to design an efficient plant extraction process. This includes creating a custom database of material absorption capacity, absorption rates, impurities fraction, and liquid entrainment. OLI consultants can also design the purification step, producing Li2CO3 and LiOH, while simulating LiCl electrolysis. Furthermore, OLI technology can predict the effects of impurities on LiOH purity.
Hard rock lithium extraction
OLI consulting offers a range of services for from b-spodumene through to the final LiCO3 product, designing processes that optimize chemical addition and reduce overall costs. OLI can also focus on designing better chemical recovery processes, minimizing energy and new chemical consumption. Our expertise in engineering chemistry enables us to develop novel ideas and optimize operating parameters like temperature, pH, and unit operation.
Lithium from clays
OLI can assist in designing an efficient and flexible separation process for extracting lithium from clays. By predicting the behavior of all elements in every part of the plant, OLI can optimize lithium yield and purity while maximizing impurities removal. Our software's expandable database also enables users to incorporate specialty supplier chemicals without the need for expensive bench/pilot-scale testing units, providing a cost-effective and time-saving approach for testing new process capabilities.
Lithium engineering chemistry services
OLI lithium consulting includes the following services:
OLI's team of experts can help identify the causes of reduced performance and mitigate process problems, provide alternative designs to increase yield and purity and simulate the mass/energy balance, chemical requirements.
OLI experts study the brine feed or process streams to identify optimal reagent requirements or causes of unwanted impurities.
.
Existing plant operations optimization
OLI experts recreate existing plant operations using simulation software, and identify root causes for lost yield, additive inefficiencies or other process problems
Improved performance
Deliver an analysis of the current operations, including locations where Li is lost, the chemical causes of reduced performance, and how these problems can be mitigated.
Reduced costs
Provide alternative designs that show where yield and purity can be increased or where changing additives can improve costs.
Working in partnership
OLI works alongside the EPC design staff to simulate initial and revised design ideas. We will create the general layout of the plant and simulate the mass/energy balance, chemical requirements, and overall product yield/purity.
FEED
OLI Systems collaborates closely with FEED staff to assess the impact of design changes and environmental variables on plant performance. In addition, we analyze the effect of varying lithium feedstock on product output and plant efficiency. OLI also evaluates the impact of different chemicals on plant performance and provides design or operational alternatives that make these changes viable.
Our expertise in electrolyte thermodynamics and engineering chemistry allows us to provide a comprehensive analysis of these factors and offer practical solutions to optimize the lithium extraction process.
What our clients say...
OLI Systems has been the leader in electrolyte thermodynamics for over 50 years. Working across industries and bring both a broad understanding of engineering chemistry processes and a deep understanding of electrolyte thermodynamics. As consultants, we have mastered the methodology and expertise to understand and address water-based operations.
"OLI's Consulting Services helped us achieve efficient plant design and regulatory approval. Their accurate mass balance based on our goals reduced costs and increased operational efficiency. Their consultants assisted with process changes and provided software licenses and training to improve the process throughout the project life cycle"
Accurately predicting mass balance plantwide
Predicting the chemical reactions and retention of DLE absorbents
Predicting when solids will form and how to enhance or prevent them (depending on goal)
Minimizing water and chemical requirements to plant
Calculating product purity based on a complete brine composition assessment
Addressing regulatory questions and requirements using first-principles thermodynamic software
Simulating specialized units like RO, ion exchange, and electrolysis
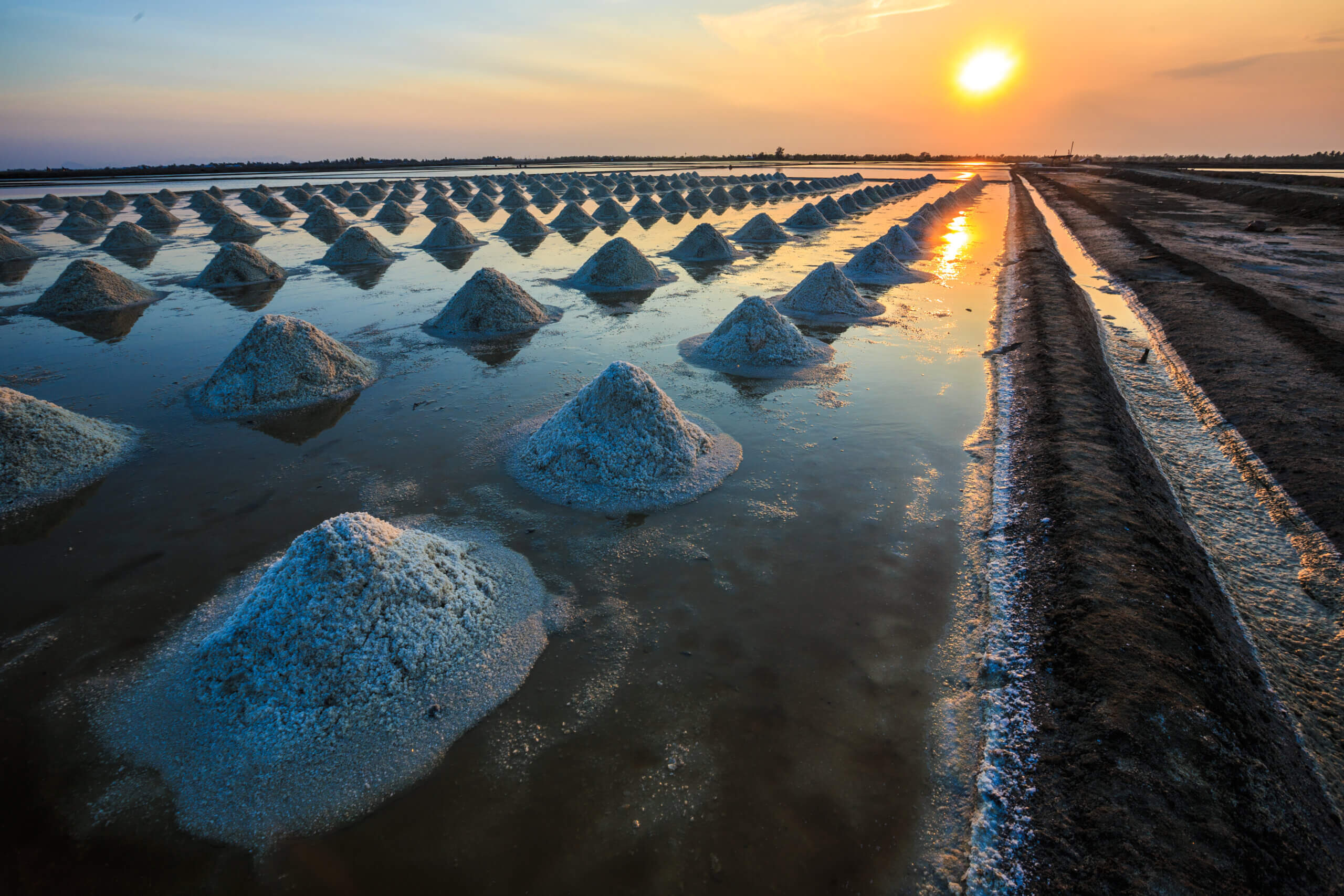
RELATED RESOURCES